Without a structured BOM management software, manufacturers struggle with version control issues, disconnected processes, and inaccurate inventory tracking, resulting in cost overruns and production bottlenecks. The challenge intensifies when businesses need to integrate BOM with procurement, inventory, and ERP systems for seamless operations.
This blog explores the critical role of BOM management software, key features that ensure a streamlined and scalable process, and how manufacturers can overcome common challenges associated with BOM management.
What is a Bill of Materials (BOM)?
It serves as a blueprint for production, ensuring that manufacturers have a clear understanding of what materials are needed, in what quantity, and order to assemble a finished product. Often referred to as a product recipe, assembly list, or component list, a BOM plays a critical role in production efficiency.
In manufacturing, having an accurate and well-structured BOM is essential for streamlining production planning. It helps manufacturers plan material requirements, manage inventory, and track production costs, ensuring that there are no material shortages or production delays. By defining the right parts and quantities, a BOM helps reduce material wastage and optimize production efficiency.
Moreover, a BOM provides better production visibility, allowing manufacturers to predict potential delays, adjust material orders, and control overall production costs. It plays a vital role in the Material Requirements Planning (MRP) process by helping businesses determine what materials are needed, when they are needed, and in what quantity — ensuring smooth procurement, production and fulfilment flow. This reduces material shortages, avoids production halts or order delays and minimizes overstocking.
Whether it’s ensuring smooth production flow, minimizing waste, controlling costs, or streamlining the MRP process, a well-structured BOM is the key to efficient manufacturing planning and execution.
Types of Bill of Materials (BOM)
Understanding the different types of BOMs is crucial for streamlining production processes. Here are some commonly used types:
- Engineering Bill of Materials (EBOM)
The Engineering BOM is created during the product design phase and contains the technical components and assemblies required to build a product. It is typically generated by CAD (Computer-Aided Design) systems and includes detailed specifications, part numbers, and engineering drawings. EBOM serves as a reference for design validation and assists in planning manufacturing operations. - Manufacturing Bill of Materials (MBOM)
The Manufacturing BOM focuses on the production process, listing all materials, components, and assemblies necessary for manufacturing a finished product. It often includes information on packaging, labels, and additional items required during assembly. Unlike the EBOM, the MBOM incorporates factors like production tools, workstations, and routing steps, ensuring seamless coordination between engineering and manufacturing teams. - Configurable Bill of Materials (CBOM)
A Configurable BOM is used when manufacturing products with customizable options. It allows companies to define multiple product variants based on a set of pre-defined components and configurations. CBOMs are widely used in industries with make-to-order or assemble-to-order processes, enabling manufacturers to efficiently manage different product versions without creating separate BOMs for each variation.
Structure of BOM
Single-Level BOM
A Single-Level Bill of Materials (BOM) is a straightforward list that contains all the components, parts, and materials required to manufacture a product. It does not break down any subassemblies or internal components, making it suitable for simple products with a clear and direct assembly process.
For example, a skateboard manufacturer purchases four components—Deck, Sticker, Warranty Card, and Transfer—from suppliers, assembles them in-house, and sells the finished skateboards. The Deck is the major component in this case, and when sourced from a dedicated supplier along with the other parts, it simplifies the manufacturing process. Since these components are simply assembled without any intermediate subassemblies, the skateboard follows a single-level BOM structure. This makes the production process straightforward, with all parts being directly accounted for in one stage.
However, for more complex products that require multiple stages of assembly, a Multi-Level BOM is often preferred to provide better visibility, control, and accuracy in production.
Multi-Level BOM
A Multi-Level Bill of Materials (BOM), also known as an Indented BOM, is a hierarchical structure that provides a detailed breakdown of components, subassemblies, and final products. Unlike a single-level BOM, it captures each stage of production, allowing manufacturers to clearly define parent and child components involved in the manufacturing process. This ensures better traceability, cost management, and production control, especially for complex products.
What is a Sub-assembly?
A sub-assembly is an intermediate product made up of several smaller sub-components, which can either function as a standalone product or be used as a part of a larger final product.
Sub-assemblies are critical in manufacturing as they:
- Simplify production: Prebuilt parts can be directly added to the final product, reducing production complexity.
- Enhance traceability: Defects can be quickly traced to a specific sub-assembly, minimizing production disruptions.
- Reduce lead times: Manufacturing critical components in advance reduces production downtime.
To better understand multi-level BOM, consider the manufacturing of a skateboard:
- Finished Product: Skateboard
- Components: Sticker, Warranty Card, Transfer, Deck (sub-assembly)
- Deck: Glue, Face, Ply, Core
In this example, the Deck is a component that is manufactured in house using Glue, Face, Ply, and Core, hence it can be called an intermediate product. Once assembly of the Deck is complete, it is combined with Sticker, Warranty Card, and Transfer to manufacture the skateboard, which is the final product. This hierarchical structure streamlines production by breaking down the skateboard into manageable sub-assemblies, making it easier to track materials, monitor progress, and identify issues at each stage. It also improves traceability by providing a clear view of each component’s origin and assembly process, allowing manufacturers to efficiently manage inventory levels and ensure smooth production flow.
Additionally, sub-assemblies can serve a dual purpose — they can be sold individually as separate products or used as a component of another larger product. This approach offers greater manufacturing flexibility and reduces operational inefficiencies.
A Bill of Materials acts as the foundation for efficient production planning, allowing manufacturers to minimize errors, control costs, and improve overall production efficiency.
What is BOM Management?
BOM management refers to the processes and strategies used to manage a business’s Bill of Materials efficiently. It involves collaboration between teams, ensuring seamless communication between various stakeholders such as engineers, procurement teams, and production staff.
An effective BOM management process ensures that everyone involved has real-time access to essential data, helping streamline production and improve overall product quality.
Challenges in BOM Management
- Frequent Design Changes: Frequent changes in BOM can lead to the wrong parts being used in production. For example, in the automotive industry, modification to a vehicle’s design—such as a change in material, component specification, or supplier—requires immediate BOM updates to ensure production accuracy. Without a structured change management process, outdated BOMs can lead to incorrect part procurement, production delays, and quality issues.
- Complexity of Multi-Level BOMs: Many manufacturing industries involve highly intricate multi-level BOMs, where a single finished product consists of thousands of components. Managing these hierarchical structures is challenging, as any modification at one level can impact multiple interconnected parts. Additionally, the lack of visibility and searchability within large BOMs makes it difficult for teams to locate specific components quickly. Ensuring consistency across different levels while tracking dependencies, suppliers, and material requirements requires robust BOM management systems.
- Version Control Issues: Managing multiple versions of a BOM is critical where frequent design updates lead to constant revisions. Without a robust version control system, different departments may work with outdated BOMs, resulting in incorrect part procurement, assembly errors, and production delays. Inconsistencies between engineering, procurement, and manufacturing systems can lead to costly rework and compliance risks. Establishing a centralized, well-documented version control process ensures that only the latest, approved BOM is used, preventing miscommunication and operational disruptions
- Seamless Integration with ERP: Integration between BOM management and ERP (Enterprise Resource Planning) systems is essential for efficient production. Changes in BOM data need to sync with ERP. A poorly integrated system can lead to data mismatches, where engineering teams update BOMs, but procurement and manufacturing teams continue using outdated information from ERP. This disconnect can cause incorrect material orders, production delays, and cost overruns. A well-synchronized integration ensures real-time updates, accurate material planning, and smooth coordination between design, supply chain, and production teams.
Benefits of Effective BOM Management Software
As we have seen, challenges like frequent design changes and version control issues can lead to miscommunication, procurement delays, quality issues, and a host of other problems that any business would want to avoid. An effective BOM management software can help overcome these challenges by ensuring real-time updates, seamless integration, and improved coordination across departments. Let’s explore the key benefits of BOM management software and how it streamlines production, reduces errors, and enhances efficiency.
- Real-time BOM Updates & Version Control: An effective BOM management software ensures that all teams—engineering, procurement, and production—are always working with the latest version of the BOM. With real-time updates, any design modifications or part changes are instantly reflected across all systems, reducing the risk of outdated information leading to incorrect orders or assembly errors. Robust version control helps track revisions, maintain historical records, and prevent miscommunication, ensuring a smooth and error-free production process.
- Seamless Integration with ERP: A well-integrated BOM management software ensures seamless synchronization with ERP systems, enabling accurate material planning, procurement, and production scheduling. When BOM updates automatically reflect in the ERP, procurement teams can order the right parts, inventory levels stay optimized, and production timelines remain on track. This eliminates manual data entry, reduces the risk of human errors, and ensures data accuracy across the organization. By maintaining an always-updated BOM in the ERP system, manufacturers can prevent costly delays, reduce wastage, and enhance operational efficiency.
- Better Supplier Coordination: BOM management software enhances supplier coordination by automatically updating purchase orders whenever a BOM modification occurs. When a design change impacts component requirements, the system instantly reflects these updates in procurement workflows, ensuring that suppliers receive accurate part specifications and quantities. This eliminates the risk of ordering outdated or incorrect materials, reduces manual intervention, and accelerates the supply chain. By keeping suppliers aligned with real-time BOM changes, manufacturers can prevent delays, reduce excess inventory, and maintain a seamless production flow.
- Enhanced Multi-Level BOM Handling: Multi-level BOMs consist of complex sub-assemblies and components, making accurate tracking essential. An effective BOM management software ensures that changes at any level are automatically updated across all dependent components, reducing errors and misalignment. It provides a clear hierarchical structure, helping production teams manage dependencies, avoid missing parts, and optimize assembly workflows. With real-time visibility into multi-level structures, manufacturers can improve efficiency, reduce rework, and ensure smooth production operations.
- Cost Optimization, Inventory Control & Faster Production: An effective BOM management software helps manufacturers optimize costs by providing real-time visibility into material expenses and alternative sourcing options. It prevents overstocking and shortages by ensuring accurate inventory control, reducing waste, and avoiding unnecessary procurement costs. Additionally, automating BOM updates minimizes manual intervention, reducing errors in production and ensuring that the right parts are used every time. This leads to faster production cycles, fewer delays, and reduced rework, ultimately improving efficiency and profitability.
Choosing The Best BOM Management Software
BOM management is often a part of Manufacturing Execution and Planning Systems (MEPS), enabling manufacturers to efficiently manage materials, production processes, and inventory. Selecting the right BOM management software is crucial for improving manufacturing operations and minimizing production inefficiencies.
Here are some key factors to consider when choosing a BOM management software:
- Feature Overlap & Customization Needs: When selecting BOM management software, it’s essential to evaluate how well its features align with your specific requirements. If a software solution provides 100% feature overlap, it’s an ideal choice. However, if no software meets all your needs, compare different options to find the one with the highest overlap. In niche industries, where standard software may offer less than 80% overlap, customization becomes necessary. In such cases, open-source software is preferable, as it provides greater flexibility for modifications. On the other hand, if a SaaS solution fully meets your needs, it’s often the better choice due to ease of deployment and maintenance. Analyzing feature overlap ensures you invest in software that best supports your production processes while minimizing unnecessary custom development efforts.
- Consumer-grade User Experience: A BOM management software should have an intuitive user interface that simplifies BOM creation, modification, and navigation. In industries dealing with thousands of materials and complex multi-level BOMs, robust search functionality is essential, allowing users to quickly locate components without sifting through endless records. Many legacy systems lack a modern, consumer-grade user experience, leading to steep learning curves and high training costs. A well-designed UI improves adoption rates, reduces onboarding time, and enhances overall efficiency, ensuring that teams can focus on production rather than struggling with software usability.
- Support for Custom Dashboards & Reporting: Manufacturers often require custom dashboards and reports to gain insights tailored to their specific operations. Many SaaS-based BOM management solutions offer out-of-the-box (OOTB) reports, which can be useful if they meet your needs. However, if OOTB reports are insufficient, the software must provide the flexibility to build custom dashboards and reports. Before selecting a solution, it’s crucial to ask the vendor about the effort required to create new reports and whether the system allows easy customization. Conducting a proof of concept (POC) by developing one or two custom reports can help evaluate the software’s capabilities and ensure it meets your reporting requirements.
- Scalability & Security: A BOM management software should be scalable to support your growing production needs, whether you are managing a few hundred components or handling complex multi-level BOMs with thousands of parts. The software must efficiently handle increasing data volumes, users, and integrations without performance degradation.
Additionally, security is critical, as BOM data contains sensitive manufacturing information. The system should offer role-based access control (RBAC) to restrict unauthorized modifications, data encryption to protect confidential information, and audit trails to track changes. Whether choosing an on-premise or cloud-based solution, ensuring scalability and robust security measures will help safeguard your data while allowing room for future expansion.
There are numerous BOM management software tools available in the market, ranging from proprietary solutions to open-source alternatives. Some of these tools are specifically designed for BOM and manufacturing management, while others are integrated within larger enterprise solutions, such as ERP (Enterprise Resource Planning) systems. Additionally, while certain software provides basic, industry-agnostic features for general manufacturing processes, others are highly specialized, catering to specific industries like automotive, electronics, or pharmaceuticals. Given the vast number of options, the following selection is not exhaustive but highlights a few popular mid-market, manufacturing-focused solutions that are widely adopted for manufacturing planning.
1. Katana
A SaaS solution designed for small to mid-sized manufacturers, Katana provides essential BOM management features but lacks deep customization capabilities. As a cloud-based platform, businesses have limited control over data storage and system modifications. Its scalability is restricted, making it less suitable for manufacturers with complex production workflows that require software tailored to their specific business needs. [Reference]2. Tulip
A no-code/low-code platform focused on streamlining shop floor operations with customizable applications, including BOM management. However, it lacks robust data control, making bulk updates and seamless data access challenging. Users have reported poor data fidelity, difficulty in managing complex data models, and limited customization options. These shortcomings make Tulip less suitable for large-scale manufacturers that require advanced data analytics, structured reporting, and adaptable software for evolving production needs. [Reference]3. Plex
A cloud-based manufacturing execution system known for real-time inventory tracking and production management. However, it relies heavily on IT support for setup, reporting, and system configurations, making it difficult for non-technical teams to operate independently. Users have also reported delayed issue resolutions, poor data accessibility for legacy features, and limited flexibility in adapting to new workflows. These constraints reduce its agility, making it less ideal for businesses requiring quick adaptability, seamless operational control, and long-term customization. [Reference]4. Apache OFBiz
An open-source business automation platform that provides the foundational building blocks for developing a customized Manufacturing Execution and Planning System. It is industry-agnostic, offering a generic framework that businesses can tailor to their specific industry needs. With its built-in MEPS solution, manufacturers can seamlessly manage BOM, production planning, inventory, and procurement within a unified platform. Unlike proprietary software that often limits flexibility, Apache OFBiz provides greater control, scalability, and ownership, making it an ideal choice for companies requiring extensive customization.
If your business requires custom BOM management software that can scale with your growing production needs, HotWax Accelerator is worth considering. It combines the flexibility of Apache OFBiz with pre-built solutions for order management, warehouse management, and manufacturing planning, ensuring faster implementation and enhanced operational control.
Conclusion
At HotWax Systems, we specialize in delivering custom business applications built on top of Apache OFBiz. To learn more about our services on Apache OFBiz Development and Consulting, click here.
Our flagship offering HotWax Accelerator, extends the capabilities of native Apache OFBiz with:
- Modern consumer-grade UI for seamless user experience.
- Advanced search with Apache SOLR for faster and smarter data retrieval.
- Pre-integrated tools like Apache Superset for real-time analytics and custom reporting.
- Seamless integrations with existing enterprise systems.
Whether you need a comprehensive MEPS solution or a unified system combining Procurement Management, OMS, WMS, and MEPS, HotWax Systems can build, configure, and customize Apache OFBiz or HotWax Accelerator to meet your unique business requirements.
Connect with us today to explore how HotWax Accelerator can streamline your manufacturing operations and improve overall efficiency.
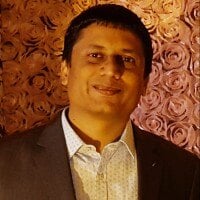